Constellium – Circular and Constant Aluminium (CirConAl)
Developing lower carbon, lower cost recycled aluminium extrusion alloys
Constellium aims to develop the lowest embodied CO₂ content aluminium alloys helping automakers reduce the carbon footprint of their products. The project will look at designing, developing and testing aluminium automotive components at scale to demonstrate that high-strength alloys with high-recycled content can meet or exceed OEM key performance criteria, such as strength, crushability and durability.
The project consortium will also develop scrap sorting technologies to ensure valuable metal is recycled into new automotive solutions, contributing to a circular economy.
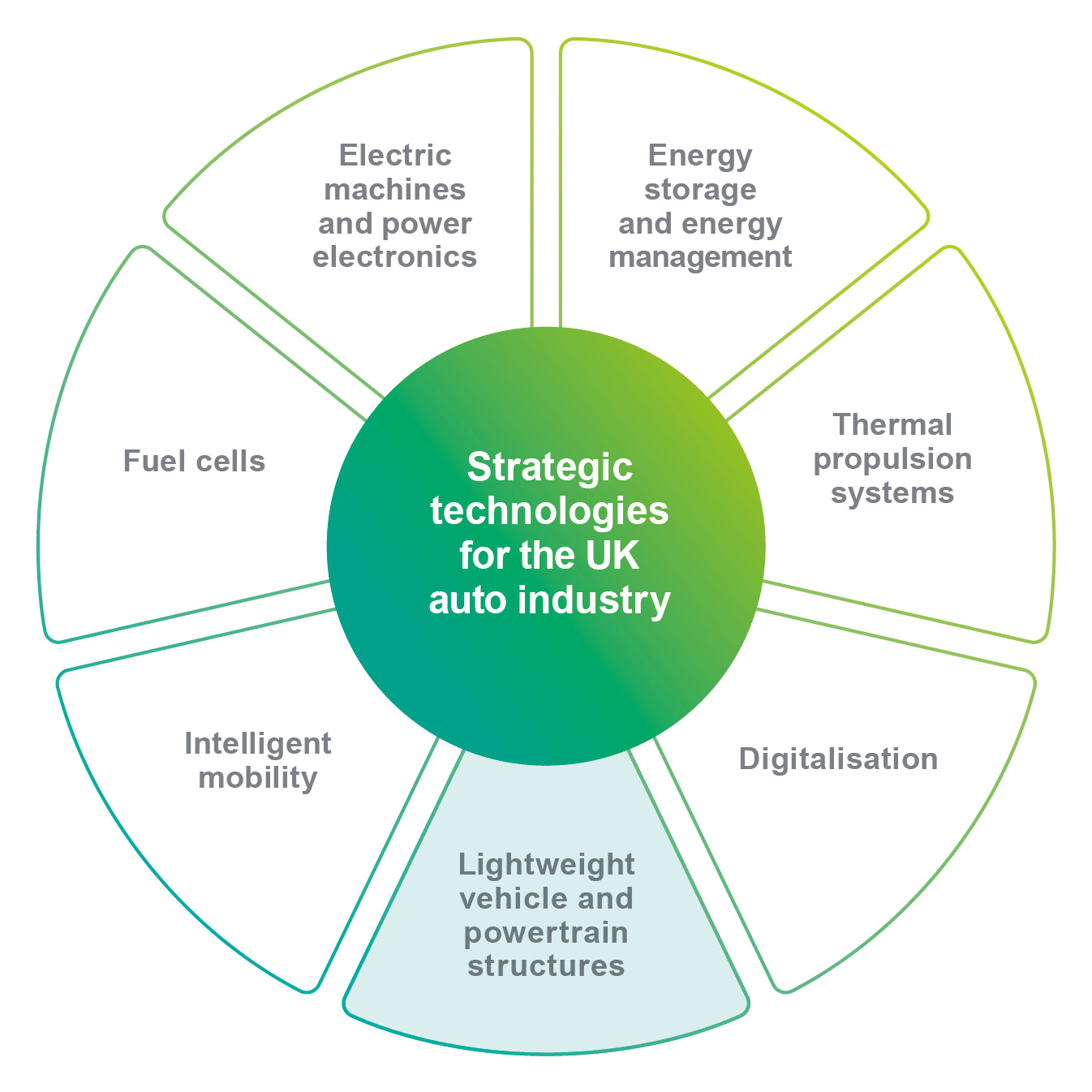
Ultra-low embodied carbon manufacturing for aluminium alloys
Project highlights
- Using targeted sorting, blending and refining technologies as the main metal input to a state-of-the-art automotive billet cast house, producing a new generation of highly recyclable aluminium alloys.
- Developing scrap sorting and blending technologies to ensure valuable metal is recycled rather than downcycled
- Validating low embodied CO₂ aluminium solution, weight and cost savings, demonstrating capacity to outperform virgin aluminium alloys.
- Working with BMW and Gordon Murray Design for design optimisation and product application
- Shortening of the supply chain due to current dependence on global shipping for primary aluminium supply
- Total project value £10 million, with £5 million funded through the APC.
Project consortium
- Constellium, Uxbridge
- Brunel University London, Uxbridge
- University of Warwick, Coventry
- Milver Metal Company, Coventry
- Innoval Technology, Banbury
- Scanmetals Ltd, Wolverhampton
- BMW Motorsport, Hampshire
- Gordon Murray Design, Surrey
- Cupral Group, Middlesbrough